Your Quality Management is Failing and Here’s Why
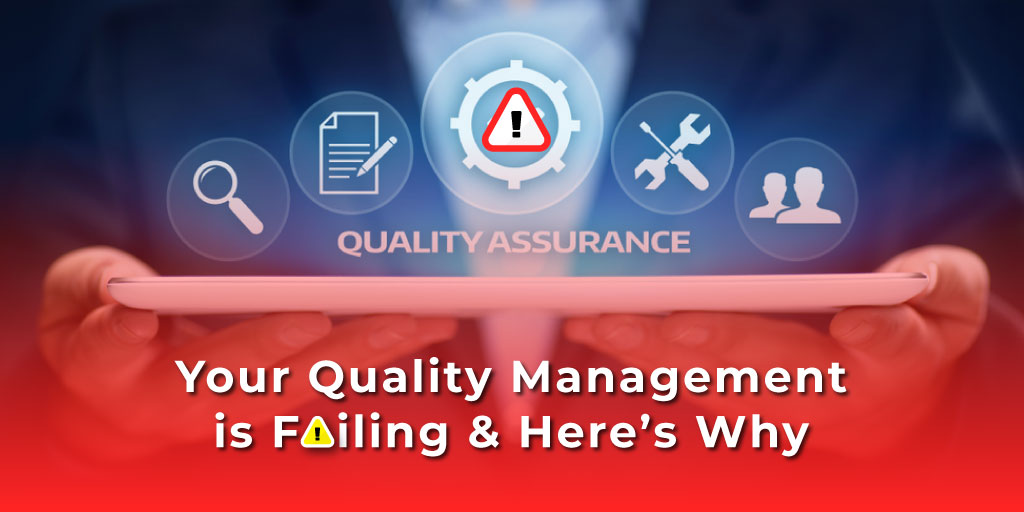
Article Context:
Earlier this year, I lived by a legit rocket scientist for nearly 30 years. This guy was amazing, beyond the obvious reasons! He was very conversant, generous, a helping hand, and even an ecclesiastical leader for our church, carving out an extra 20 hours per week to help his congregation. He had some stories from his rocket scientist days. Most of these stories he was not able to share since most were classified as Top Secret. He worked indirectly for Thiokol, an infamous name for rocket propulsions, namely, the Challenger Space Shuttle explosion.
Above was a horrific example of failed Quality Management Process. Again, my former neighbor wasn’t involved with this, but he knew people who were, sadly.
The hardware failure of a solid rocket booster (SRB) ‘O’ ring was cited as the immediate, mechanical cause, but human culpability lay behind the launch’s decision-making process.
Thiokol, the subcontractor behind the ‘O’ rings’ supply, warned NASA of the potentially adverse effects of cold temperature on the ‘O’ rings performance a day before launch. Engineers conceded that the database behind the ‘O’ rings quality testing program could be corrupted and recommended waiting till outside air temperatures reached 53®F before proceeding with the launch.
This concern was met with outrage by NASA officials, who were wary of another delay’s political and financial repercussions. It was at this point that Thiokol ended a video live link so officials could confer amongst themselves. The chief engineer at Thiokol was advised to put his ‘management, not engineering cap on.’ Five minutes later, the supplier re-joined the GDSS and ratified the launch. Sadly, the rest is history.
https://www.processexcellencenetwork.com/lean-six-sigma-business-performance/articles/5-quality-failures-that-shook-the-world
In the pharma, med device, and manufacturing world, better QMS process & systems are in place to avoid such grievous scenarios. So please make sure to look out for the following within your company:
Standard Operating Procedures
Whether your business model is for product or service, following a consistent QMS process helps ensure a compatible end product. You’re expected to follow specific procedures to ensure quality, even in creative fields, especially if the results don’t stand up to close inspection.
Problem-Solving Procedures
If and when a problem comes up, how do you go about solving it? Are there dispute-resolution procedures for disagreements between staff members? What are the guidelines for reporting an issue?
Maintain ISO Compliance
ISO 9001 Standards require companies to set up processes to determine customer requirements, and these requirements then need to be known to everyone else in your organization. Track and analyze customer satisfaction with direct relevance to customer relationship management. To meet these standards, you need to pursue customer feedback and make changes to solve any issues they might raise.
Ensure Employees are Properly Trained
Employees need to have sufficient delegation, communication, and skills to build and implement proper processes. The best starting point here is to ensure you have appropriate training systems on quality management software and verify that all employees are on the same page, focusing on quality control. Reasonable quality control starts here.
FAQ's
Why does quality management fail?
Quality Management deficiencies can happen due to the manufacturing process, intended or unintended changes in procedures, implementation faults, changes n ingredients or raw materials or suppliers, and human errors. All these together or individually may constitute a quality management failure.
What are the most common failures in quality management?
- Lack of training for employees
- Lack of processes and procedures
- Lack of communication of collaboration
- Lack of proper Change control methods
- Lack of risk assessment
- And Lack of centralized Quality Management System
What are five areas that can ensure quality performance?
Employee involvement and improvement
Employees are responsible for maintaining quality and could not achieve continuous quality improvement without the leadership team’s involvement in training the required skills. Every employee has the ability and responsibility to deliver quality products. Quality is not an individual job, and it is the core component of the culture which is to be owned by everyone in the organization
Process-Based Approach
The process-based approach is the core component of FDA and ISO quality management regulations because consistent quality results are achievable when processes and procedures are interrelated.
Integrated Quality System
The quality management system consists of interrelated quality frameworks that help organizations optimize product and processes quality performance adhering to compliance and regulations. Additionally, QMS enables user-friendly UI, e-signatures, configurable workflows, non-editable audit logs, and scalable without requiring resource-intensive revalidation.
Continuous improvement
Life science industries are meant to meet strict guidelines and regulatory requirements and meet changing customer expectations. A strategic approach to improvement can allow organizations to sustain market trends, meeting standards and regulations consistently. The strategic process should involve developing employees’ skills, internal process efficiencies, and meeting customer expectations and market requirements. A centralized system like Quality Management Software can ensure continuous improvements by tracking the process deliverables, accessing training performance, analyzing risk factors, and auditing progress meeting quality standards.
Evidence-based action plan
To drive quality improvements and address Nonconformances and CAPA requires practical investigative information and analytics determining the root cause of the issue. Action plan based on the analytics and evaluation of potential information produces desired results. A QMS system should provide investigation methods and analysis identifying the possible patterns of the root causes to help the quality unit and leadership identify the issues among SOP changes, manufacturing shifts, or other factors. In addition, Quality Management Systems provide transparency of processes and outcomes to measure impact.