How Training Management System helps to ease the training in Life Sciences Industry ?
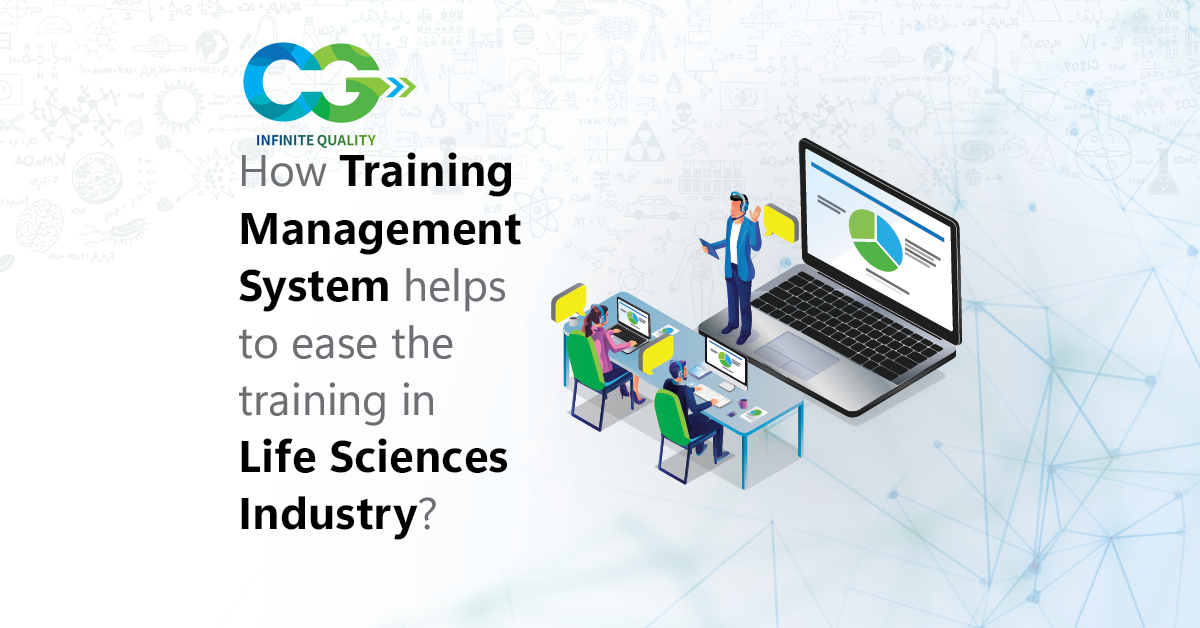
Article Context:
- Training Management System
- FDA Quality System Regulations
- Training requirements outlined by FDA
- How does a training management system help ease training?
Training Management System
In the life sciences, industries like pharmaceuticals, medical devices, biotechnology, food, and drug manufacturing companies traditionally use paper-based and legacy systems to document employee training progress and training processes. For a smaller company, it may not be critical to schedule training plans and document training progress. Still, it becomes crucial as the company grows to a mid-level or enterprise level. Paper-based processes and legacy systems are inefficient for several reasons. The most significant reason is the failure to maintain paper-based training plans and individual employee training progress. As the life science regulated industry, the company should establish the employee training requirements and be trained appropriately to carry forward the process and procedures as regulated. The organization can prove this by maintaining the training records.
An automated Training Management System facilitates the organization of a streamlined process with documentation for easy access, assignment, monitoring, and management of the training process until it is completed. Automating the training needs requires digital integrated quality management (QMS) – document management (DMS) – training management system (TMS). A closed loop quality system integrated with DMS and TMS can streamline the training process through quality events and documents. This ensures a trained workforce and scalable growth that meets compliance and industry regulatory standards. The outdated training management tools, legacy systems, and traditional paper-based systems lack efficiency and make internal and external audits difficult and cumbersome.
FDA Quality System Regulations
The FDA’s quality system regulations leave an open-ended solution for the companies regarding how they intend to handle training in meeting those regulatory requirements. The FDA’s basic interpretation is that the employees appointed must know their job roles and functions and are trained based on their roles on the SOP (Standard Operating Procedures) for performing the tasks and verification – validation training for identifying the defects and errors. Their training progress is tracked, monitored, and recorded with evidence of training.
Quality is not a one man’s job, it is everyone’s job, so the organization should ensure that the person has relevant training to contribute to the quality objectives and achievements. And that does not mean that all of them should be trained on everything. It is a complex process for organizations with larger employee groups. So, the quality procedures and processes documentation that is followed in the company should have associated training. The employees, part and picture of the quality processes should be trained on those documents.
Training requirements outlined by FDA
The section of the FDA that outlines the training requirements and the quality system regulations for medical device companies is 21 CFR Part 820.25.
As per this section,
- Every medical device manufacturing company shall employ manufacturers with the required educational background, training, and experience to perform the activities correctly as specified.
- The company documents the training needs and training progress of employees/manufacturers and is trained to perform duties adequately.
- As a part of the training, the employee should be capable of identifying defects when mismanaged as a part of their job roles and responsibilities
- The verification and validation personnel should have the knowledge and training on identifying the errors and defaults when the products do not meet the defined specifications and are capable of prescribing corrective, preventive resolutions as a part of their job responsibilities.
TMS (Training Management System) in connection with Quality Management System (QMS) and Change Control Management.
To encourage the quality processes in action, the best option is to incorporate training activities within the quality management system. For example, to serve the quality purpose, the organization can have 100 pages of the document, but the employee needs to get trained on those 100 pages. Otherwise, it is not of use. Although they certainly cannot follow the documented process, they should know why, when, and how to do the steps to ensure quality. Likewise, the policies, procedures, and processes while maintaining the quality of an organization evolve and change over time. So from a training perspective, the employees involved in the process should be retrained on the changes of the updated versions. If the employees involved don’t know about the changes, there is no point in revising the processes, procedures, or policies.
How does a training management system help ease training?
With this, we understand the importance of a training management system in an organization and the challenges with a traditional system. Now, let us know why a new training tool other than the conventional methods like paper-based and legacy systems is far more efficient and why life science companies should incorporate a QMS integrated TMS for achieving quality objectives while meeting regulations and compliance.
In an intelligent training management system like TMS, streamlining training processes, planning training requirements, and tracking and recording training progress across different platforms and the organization as a centralized application is simple and easy. It will help the organization to track the progress of individual employee and their completing and in progress status with a click. TMS, a SAAS Cloud-based application, facilitates an efficient tracking system across the quality events, document triggered, and manually created training requirements in real-time.
Most importantly, the SOPs (Standard Operating Procedures) will be effective when most employees complete their training. So having automation integrating the QMS processes and document change control with the training requirements ensures transparency across the organization, increasing efficiency, and quality. Additionally, it maintains accessible controlled and uncontrolled documents for training. Also, the life science industries – pharmaceuticals, medical devices, and drug manufacturing companies must tend to preserve and document records not only of training but of product design, specifications, test executions, validations documents, etc. Hence, a TMS connecting with QMS and DMS is the best solution.
When an employee is assigned with a training requirement, in-app notifications, email alerts, and tasks are automatically triggered to notify the users of the training assigned.
The TMS is configurable, enabling the organization to create manual training requirements or trigger training through DMS, facilitating to assign, manage, and track training requirements based on user roles and departments. In addition, assessments can be conducted, evaluations of employees are recorded, and the training progress tracking is available at all times for audits.
Reports of when and to what extent the training is completed and due by employees have been generated automatically and are available and accessible for audits at all times.
To conclude, the training process is crucial for the life sciences organization. TMS is a training management software that helps companies track employees’ training progress and provide evidence of training on processes, procedures, and updated document versions with just a click. Also, it covers 21 CFR Part 11 compliant features like e-signatures, electronic records, non-editable audit trails, validations, and cloud storage of data. So, with TMS, an organization can have different views of employee training progress with the transparency of completed and outstanding training activities to managers complying with regulations.
To learn more about the TMS for life science industries to meet all your training needs at one single point, write to our SME for a demo at sales@complianceg.com
FAQ's
What is the purpose of a training management system?
A training management system (TMS) can be defined as a system that assists trainers and administrators in managing training programs. In addition, it includes features to record, track, and report on training activities.
The purpose of a TMS is to provide a centralized location for all training-related data, courses, and training sessions. This data can be used to identify trends and make informed decisions about training programs.
A TMS can also help identify training needs and resources. This information can be used to plan and schedule training sessions, as well as track trainees progress in real-time.
What are the major requirements of training management system in medical device industry?
A training management system helps instructors organize, track, and report on their training sessions.
It also helps supervisors and managers track, monitor performance and evaluate trainee progress.
What are the FDA regulations for Training Management System?
The Food and Drug Administration (FDA) regulates the use of training management systems (TMSs) in order to ensure that the training provided to healthcare workers is effective and safe. In order to be used in the healthcare setting, a TMS must be registered with the FDA.
A TMS must be registered with the FDA in order to:
-Collect and store data about the training provided
-Track the effectiveness of the training
-Provide feedback to healthcare workers about their training
How to create and document an effective training program?
There are many ways to create an effective training program. In this blog post, we’ll explore some of the most common methods and how to make them work for you.
1.Brainstorm with your team.
The first step is to brainstorm with your team about what you want to achieve with your training program. You’ll want to think about what you want your participants to learn and how you can best help them achieve that. This can be a difficult task, but it’s important to get everyone on the same page.
2.Define your goals
Once you have a good idea of what you want your participants to learn,
3.For any TMS related questions reach out to us at sales@compliancg.com