Change Control | How to Manage a Change Management Process?
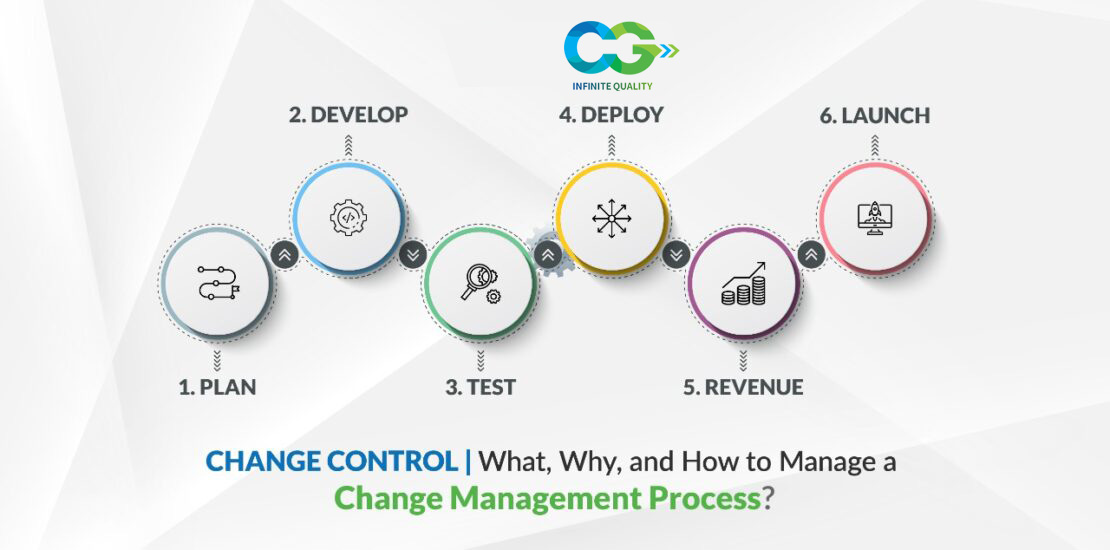
Article Context:
- Change Management
- Change Management Process
- Change Request Review
- How to Manage the Change Management Process?
What is Change Management?
Change management is when an organization creates a step-by-step protocol to manage and implement modifications to products and processes. A change management plan is a protocol that implements and executes the change management processes in an organization to embrace and encounter changes in the workflows as defined. For example, any change in the existing product feature, new product implementation, process deviation, procedural update, or controlled documents requires a change management process. In a medical device company, changes are equipment modifications related to device design control methods, techniques, formulations, procedures, labeling, or associated documentation at an operational and manufacturing level. The required documents related to the change in supplier should be in place if there is a change in supplier or raw materials used.
A change will lead to severe consequences if not handled properly. Changes can be permanent or temporary, severe or negligible, routine or emergency; it depends on how the organization mitigates the risk and addresses change implementation. Any undeclared changes may cause the company to recall the entire process or production. The change management process intervened with ISO and FDA compliance to protect public safety by ensuring the highest quality standards in the manufacturing and operational strategy of product/device development. FDA and ISO regulations specifically note undeclared changes as these are the changes that cause severe production errors.
There are various reasons for an organization to initiate a change, and those reasons are called triggers. For example, the following are the triggers of change management in a medical device company.
- Changes in the existing/new product feature that may be an enhancement or updation or failure correction lead to a change management plan
- Changes in the processes like the workflow instructions, procedures, SOP, etc
- Modifications in manufacturing units, supplier materials, or updations in the associated documents or controlled documents at a time may lead to a change management plan.
- Adjusting the product or part replacement bought up by a new customer specification leads to a change management process.
There are several reasons for product design changes to occur. However, it is overlooked for changes when a new regulation comes up, a shift in standards as laid by the company or redesigning the device per the customer specifications. No matter what the change is and how severe the impact will be, the work instructions and procedures should be updated in pre and post-market levels to align the work with compliance and run things smoothly, avoiding the cost of unplanned money and resources.
The change management process is categorized into two phases of a medical device company – Pre and Post Market Product/Device Changes.
Pre-market device design changes
The pre-market changes management process occurs in the device development stage, like when an enhancement is made to the existing product design regarding the customer specification or any replacement of the part or when a manufacturing unit or supplier or raw material is changed. So, when the organization wants to initiate a change, be it small or big, there is a need to update the device master record (DMR)
DMR is a document that details the manufacturer the device specifications like the process, procedures, and technicalities of making a device, the materials being used, its calibrations, etc. Without the DMS document, the manufacturer cannot develop the product. Hence updating this document is essential to produce the latest version of the product. Moreover, the changes in the product design during the development phase should be reflected in the DMR document by the quality team for the manufacturing team to develop the latest version in alignment with the change management process adhering to compliance. Furthermore, the quality team should ensure that changes are updated, documented, justified, and validated before the DMR gets to the manufacturing team to avoid the regulatory requirement gaps and ensure the device production still complies and is safe to use as intended.
Post-market device design changes
Post-market changes, as the word defines, once the product or device is released in the market, the change process starts with the feedback or complaint from the customer. The changes at this stage may result in improvements, enhancements, part replacement, or any cost-saving modification. Like the pre-market change process, the post-market change process includes the change update in associated documents, justification, review, approval, and validation. Pre-market changes have the privilege to proceed with the change management process without affecting the end-user safety and brand reputation. But the devices that are already in the market and the change management process raised with customer complaints or feedback will eventually affect the form function of the device and expected to implement the corrective and preventive actions before the actual change process proceeds.
Handling the change management process of the device product process
Change management process in the device production stage can occur with the inclusion of new regulatory requirements or fine-tuning of calibration units, procedural changes, adjustments in design, or replacement of manufacturing units or supplier raw materials. In brief, the change management process in an organization is raised when there is a requirement of operational and manufacturing changes in the device production process.
Change management process
To effectively document the change management, the organizations need an intelligent Quality Management System (QMS) like iQuality. The change management process starts with initiating a change request through a change request form in the QMS. The change request form in iQuality QMS is configurable as per the process in an organization to help improve the company’s change management process in adherence with compliance. The initiation of a change request happens by identifying the need for change. Then, there is a workflow tracker for the next few steps to assess the change’s risk, impact, and implementation.
Change request review
With the initiation of the change request, the quality reviews the request to determine its requirement. Then, to approve the change request further and proceed with the change management process, the quality team anticipates the benefits and impact of change.
Analyze the risk
Any proposed change, especially in the development or device production phase, must consider risk analysis. Suppose the change request regards a change in manufacturing procedure or process. In that case, the quality team should conduct a risk assessment plan to determine the impact of risk relative to the proposed change in the manufacturing process. The above statement applies when the change request is at the pre-market level. What if the device is on the market and the change request is initiated on a customer complaint. Then risk assessment should be conducted, keeping in the loop the supplier, manufacturing, and operational errors. A risk assessment will assist you in anticipating, detecting, and accounting for growth-related risks.
Update BOM (Bill Of Materials)
The most critical part of an organization’s manufacturing process is BOM. It assists in understanding the company’s requirements for manufacturing a device in which purchasers, suppliers, manufacturers, and product team know the raw materials used and their cost.
The BOM should be up to date as the slightest change in the production process may lead to shipment delays, faulty labeling, poor manufacturing process, and operational gaps. Additionally, since the BOM is associated with each material and component of the device, it should be updated with the latest information. However, the charges are unaffected by the manufacturing change. The BOM does not represent chargers or process changes; it describes the device’s going on and where the parts are located.
Manage the change management process
Minor changes should be considered for the organization’s in-depth reviews of the associated document, ensuring complete synchronization across the whole organization. To prevent adversity, change management adoption in an organization is essential, and for this, a change management system is required.
Change management requires effective team communication, adequate documentation, practical training, and an adequate turn-around time to control systematic deviations and prevent product recalls and delays.
Conclusion
Managing a change control process may seem like a simple job. However, implementing a streamlined change management process across the organization with automated workflows, approvals, and document updates is a complex task. An ineffective quality management system can cause communication gaps, non-conformances, product recalls, and non-compliance issues. Therefore, an intelligent quality management system must overcome all the above and manage the change management process. To know more about the iQMS, reach us at sales@complianceg.com.
FAQ's
What is the FDA definition of change control?
According to the FDA, change control systematically manages all changes made to a product or system. The goal of the FDA for enforcing the change control process in all life sciences industries is that changes are made that are necessary, and all changes are documented without disrupting the services using the resources efficiently.
What steps are involved within a change control procedure?
When it comes to creating a change control process, five key steps are described below. Depending on the organization and the process they follow, some methods differ slightly, but all have a few key components in common. The step-by-step process ensures that changes or modifications are streamlined to move efficiently to unnecessary changes from the request identification to the request implementation.
- Change request initiation
- Change evaluation
- Change analysis
- Implementation
- Request closure
What are the three main objectives of change control?
An effective change control process is the most critical factor in any organization to align with the Quality Management System regulations of FDA and ISO as the FDA has exceptional attention to the significant changes in the medical device-related regulations and their violation.
Changes can be classified into three main objectives:
- Changes to the Quality System, whether in documentation or specific processes/procedures
- Changes in the design of the marketable device
- Modifications to the product line.
Why should an organization implement change control?
With the change control process, the flow of information is high in an organization as it defines success metrics, streamlines workflow, allows teams to collaborate and communicate.
What are the 7 R's of Change Management?
The seven R’s of the change management process is
- Who raised the change request?
- What is the reason for the change request?
- What are the requirements of the Change request raised?
- What are the risks associated with the change?
- Who reviews and approves the change?
- What are the resources required to implement and close the change request?
- Who is responsible for the assessment and implementation of change requests?